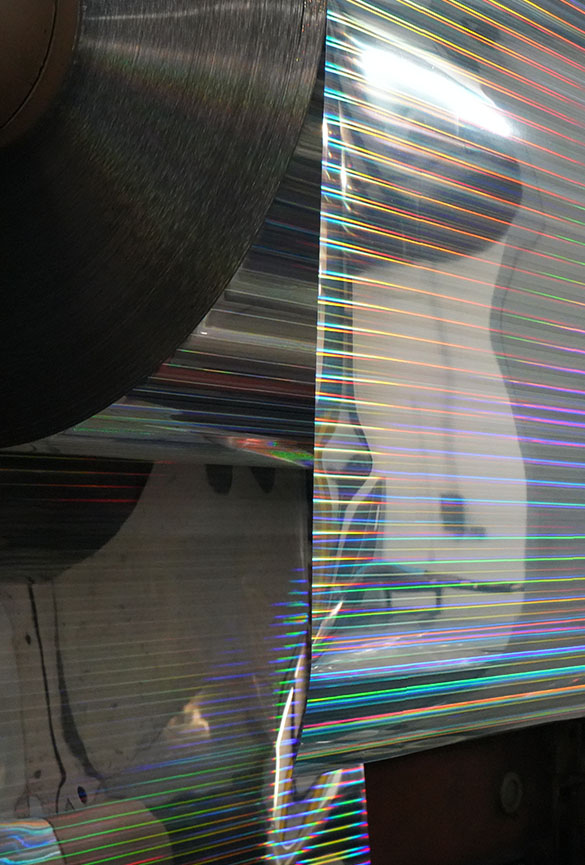
Evaporative Deposition Services
Our Evaporative Deposition Services provide a wide range of capabilities for thin film deposition using the evaporation/vapor method. With our next-generation equipment and expertise, we can accommodate web widths of up to 80 inches and thicknesses ranging from between 36GA and 1000GA (9µm to 250µm).
Using this technique, we can deposit thin layers of metal onto various substrates, including PET, Nylon, other web polymers, fabrics, and foils. Our process ensures precise control over deposition thickness and uniformity, allowing us to meet the most demanding specifications.
Whether you require decorative or functional coatings for various substrates, our Evaporative Deposition our Evaporative Deposition Services deliver exceptional results. We work closely with our clients to understand their specific requirements and provide tailored solutions that meet their unique needs.
Electron-Beam Deposition
At VDI, we utilize advanced equipment and expertise to provide Electron-Beam Deposition for various industries. Our advanced technology allows us to achieve deposition on widths ranging from 40 inches to 74 inches and thicknesses of .5 mil to 10 mil. This flexibility enables us to cater to a diverse range of applications and meet the specific requirements of our clients.
Choose VDI's Electron-Beam Deposition Services for high-tech coating solutions that combine precision, versatility, and customization, enabling your products to excel in today's competitive markets.
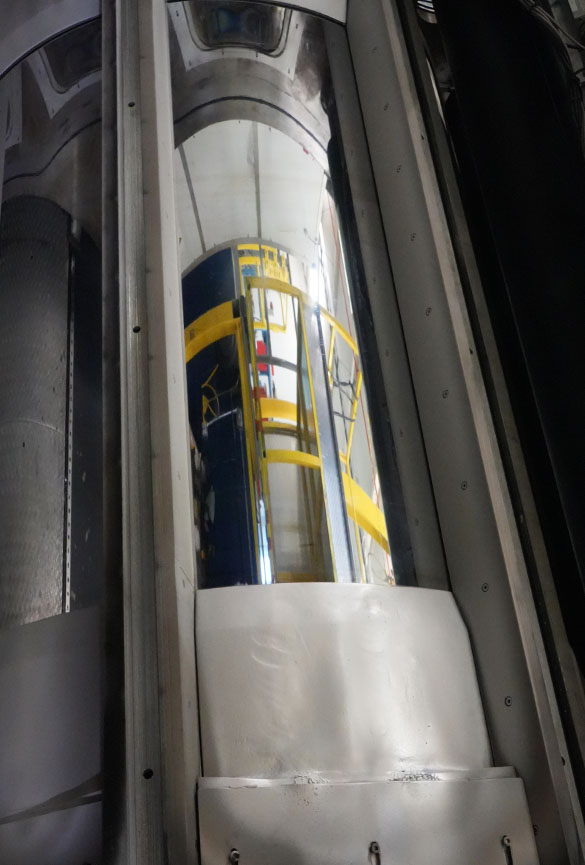
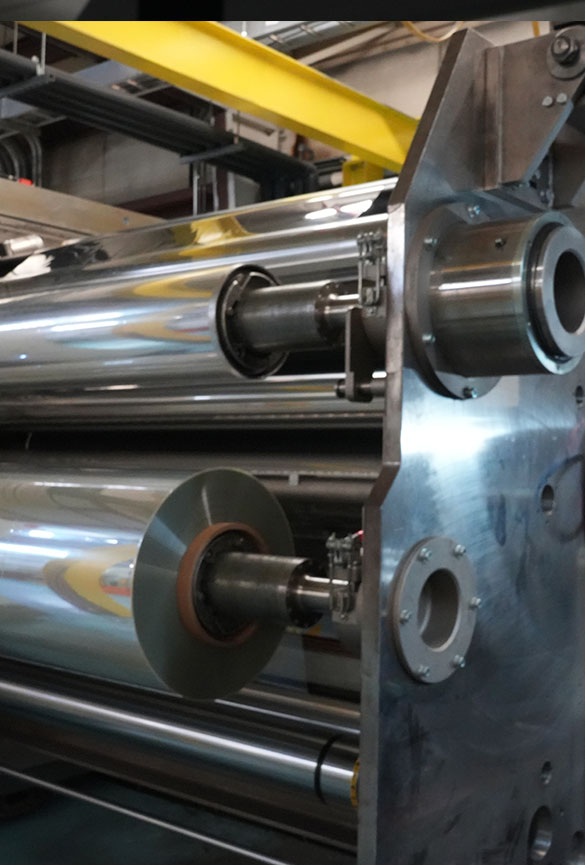
Sputtered Deposition Services
Using state-of-the-art equipment and advanced sputtering technology, we can accommodate web widths ranging from 40 inches to 74 inches and thicknesses of .5 mil to 10 mil. This wide range of capabilities enables us to serve a broad spectrum of applications, from large-scale industrial projects to microelectronics.
Using advanced equipment and advanced sputtering technology, we can accommodate web widths ranging from 80 inches to 40 inches and slit to a minimum of 4 inches. Thicknesses range from 1mm to 36GA. This wide range of capabilities enables us to serve a broad spectrum of applications, from large-scale industrial projects to microelectronics.
Partner with us for Sputtered Deposition Services that deliver high-performance thin film coatings, enabling your products to excel in functionality, durability, and overall quality.
Solution Coating & Laminating Services
Our Solution Coating & Laminating Services provide a comprehensive range of capabilities for coating, laminating, and converting films in wide-width, roll-to-roll format. With our advanced equipment and expertise, we can deliver customized film solutions that meet the specific requirements of various industries.
The Solution Coating & Laminating Services find application in diverse industries, including automotive, electronics, packaging, healthcare, and more. For example, we can provide scratch-resistant coatings for display screens, barrier coatings for flexible packaging to extend shelf life, and conductive coatings for electronic components. Our laminating capabilities enable the production of multilayer films for insulation, moisture resistance, and barrier properties.
Choose our Solution Coating & Laminating Services to benefit from our expertise in providing high-quality, customized film solutions for a wide range of applications. We are committed to delivering superior results that meet your specific needs and exceed your expectations.
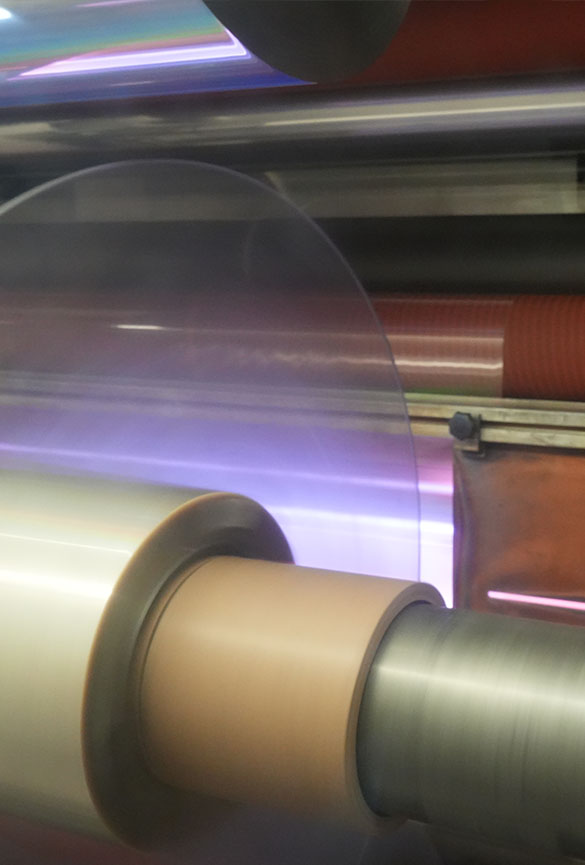
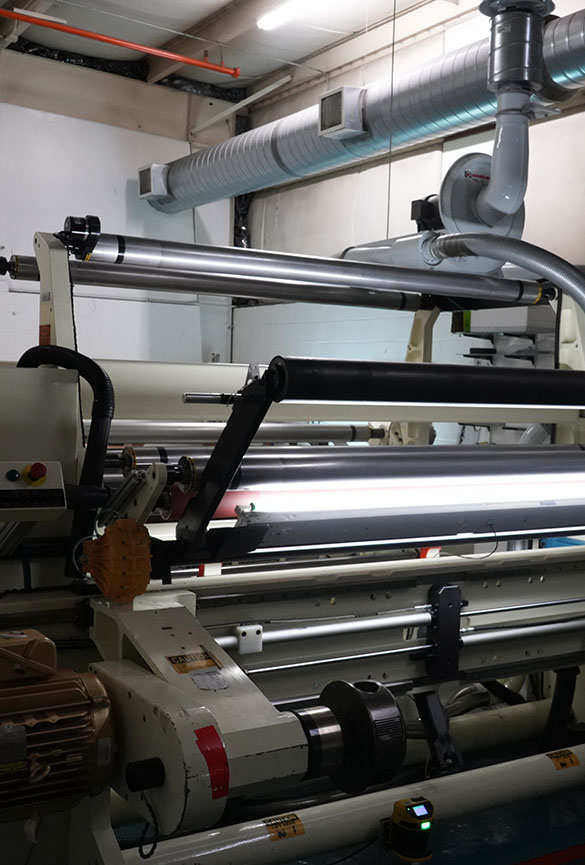
Customized Slitting and Rewinding Services
Our Customized Slitting and Rewinding Services offer precise and tailored cutting and rewinding solutions for a wide range of materials. With our advanced slitting machines and expertise, we can accommodate various widths and provide customized solutions to meet the specific requirements of our clients.
Using state-of-the-art equipment, we can handle master rolls up to 80 inches in width and cut them to the desired widths with exceptional accuracy. Our slitting process ensures clean and precise cuts, minimizing waste and optimizing material utilization. WWe can deliver the customized slitting services to meet your exact specifications.
Choose our Customized Slitting and Rewinding Services for precision cutting and rewinding solutions that meet your specific requirements. Our expertise and dedication to quality ensure that your materials are handled with utmost care and precision, resulting in superior end products.
News & Articles
Latest Blog Posts
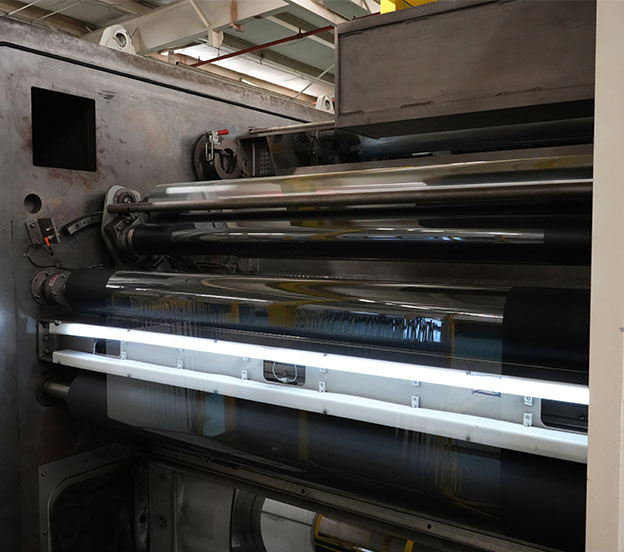
What is ITO Sputter Deposition
Indium Oxide/Tin Oxide is among one of the most heavily utilized compounds in the thin film industry due to its electrical conductivity and optical transparency.
Learn more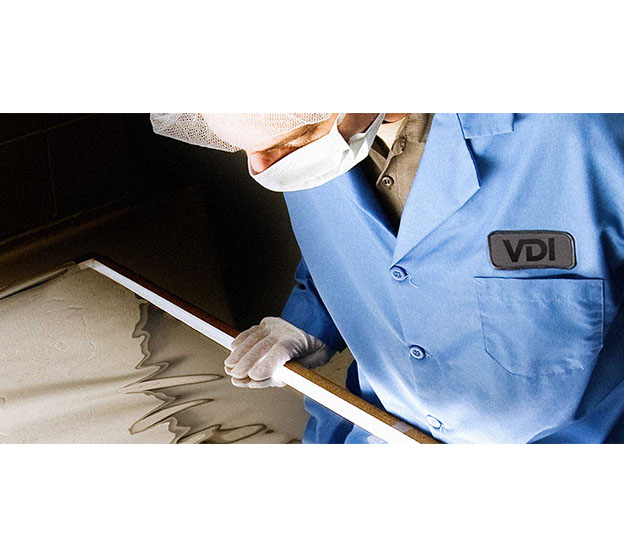
Vacuum Deposition: A Guide to Thin Film Coating Techniques
One common method for producing thin films is evaporative deposition, which involves the vaporization and subsequent
Learn more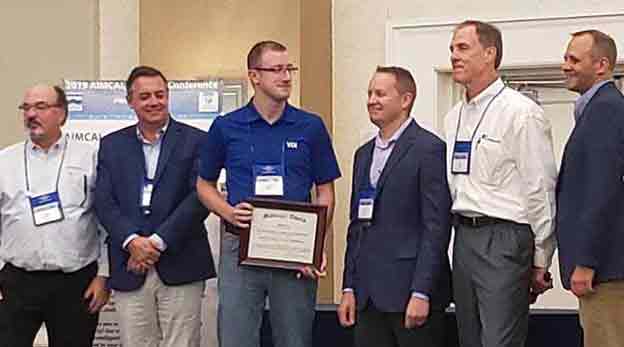
VDI’s Product Development Engineer Receives Technical Award at AIMCAL R2R Conference 2019
Rob Malay, Ph.D., Product Development Engineer at VDI, was the recipient of the John Matteucci Technical Excellence Award at this year’s AIMCAL R2R Conference 2019.
Learn more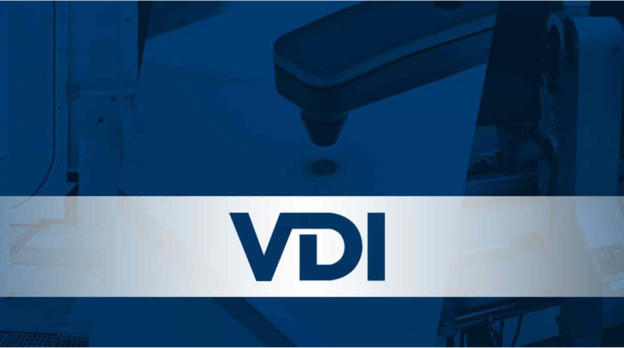
VDI Product Development Manager highlights manufacturing advances
Robert Malay, Ph.D., Product Development Manager at VDI, recently co-authored an article for Converting Quarterly entitled “Establishing the flexible-glass R2R coating ecosystem.”
Learn more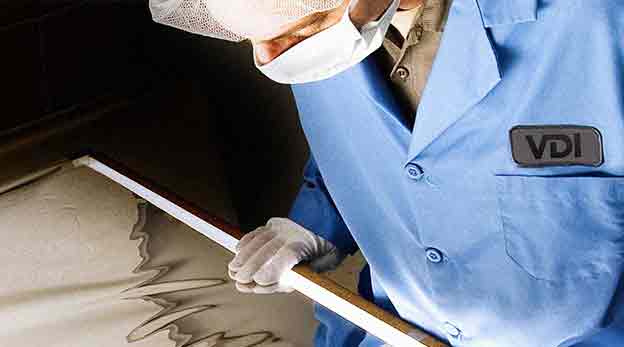
VDI Invests in New Equipment, Increases Capacity
VDI today announces a significant investment in new equipment for improved manufacturing with the purchase of a new, world-class vacuum metallizer.
Learn more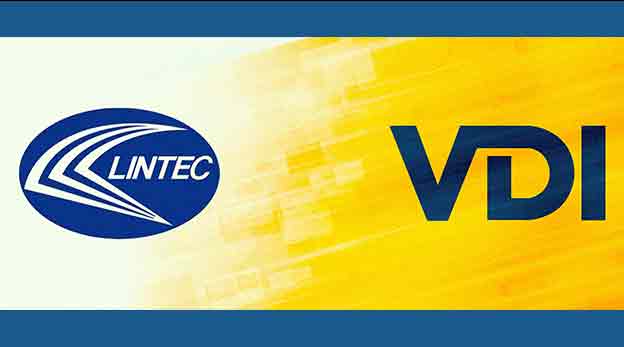
Lintec (LUSA) acquires Vacuum Depositing, Inc.
Lintec USA Holding, Inc., a subsidiary of Lintec Corporation, announced today that it has entered into a definitive agreement to acquire Vacuum Depositing, Inc...
Learn moreReady to Take the Next Step
Ready to explore how VDI's trailblazing vacuum coating solutions can elevate your products and applications? Contact us today for a free consultation with our experts.
Get a Free Consultation